Jic Fitting:
Understanding JIC Fittings: A Complete Guide
Jic Fitting Hydraulic systems are only as good as the connections are reliable. Jic Fitting Of the many types of fittings one can pick from, no other type is more solid and versatile than the JIC fittings (Jic Fitting).
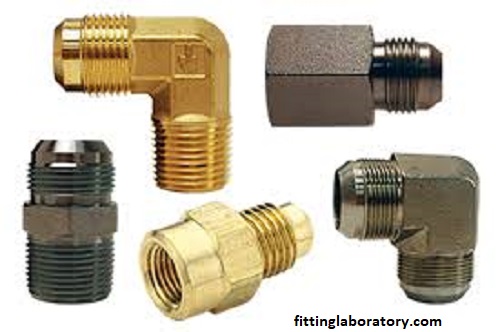
So, in the following blog post, we get down to details on JIC design, applications, advantages, and how to best use them.
What Are JIC Fittings?
Jic Fitting:
AÂ fitting, for one, is a form of hydraulic connection used in attaching hoses and tubes in fluid transfer systems. It was invented in the 1950s due to the need for standardizing hydraulic connections in different industries.
A JICÂ is famous for its flare at 37 degrees, thus sealing tight without another form of sealing substance added to it. Therefore, the nature of these types of fittings makes them best suited for high-pressure operations.
Key Features:
Jic Fitting:
- 37-Degree Flare: The distinguishing feature of JIC is the flare angle of 37 degrees. This flare angle enables the male and female fittings to mate with each other, thus tightening up the seal.
- Material Composition: fittings may be of steel, stainless steel, brass, or aluminum, depending on the demands of an application. Steel is used for applications where pressure is high whereas in low-pressure systems, brass may be opted.
- Thread Types: JIC has many different types of threads, but the SAE is the most commonly used one. This compatibility makes the fittings highly popular in many industries.
Applications of JIC Fittings:
Jic Fitting:
JIC applies itself in lots of applications. The following are some common applications.
1. Hydraulic Systems:
Jic Fitting:
The hydraulic systems operate with a high-pressure fluid transfer, and so the JIC is perfectly applied in connecting hoses and tubes in machinery, construction equipment, and automotive applications.
2. Aerospace:
Jic Fitting:
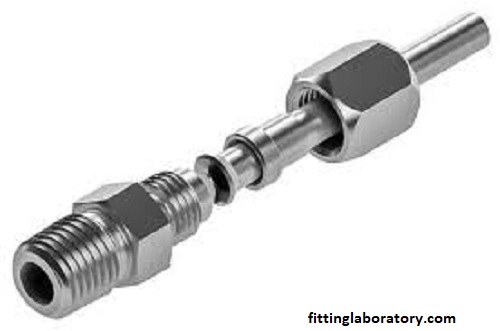
Aerocraft places prime importance on reliability and performance. In fuel systems, hydraulic controls, and landing gear systems, JIC has an application because they easily resist extreme conditions.
3. Industrial Equipment:
Jic Fitting:
Fittings are very common in industrial machines, especially for hydraulic and lubrication applications. Machines made using these fittings tend to be robust and resist pressure changes that can induce overwhelming stress on them. It is this reason why they are mainly used to manufacture equipment as well as processing machinery.
4. Car Applications:
Car applications often tend to use JIC, especially on high-performance vehicles. They are ideal for fuel lines, brake systems, and other fluid transfer applications.
5. Farm Equipment:
Jic Fitting:
In agriculture, where the equipment has to stand in grueling conditions, fittings ensure a safe connection for hydraulic systems of tractors, harvesters, and every other machinery.
Advantages of JIC Fittings:
JIC have several advantages that make them the go-to option for numerous applications:
Leak Resistance:
Jic Fitting:
The mechanical seal is created by a flare design of 37 degrees to reduce leakage chances. It’s vital in high-pressure applications as it will lead to system failure in case of fluid loss.
2. Easy Installation and Maintenance:
Fittings are designed for ease of installation. Ends with a flare that can be attached by hand and then tightened by the wrench for easier maintenance and reduced downtime.
3. Versatility:
JIC may connect hoses and tubes of various types; this makes the component applicable in several applications. The flexibility decreases the usage of different types of fittings since fewer fitting types mean less stock in inventory.
4. Long life:
Jic Fitting:
Fitting is made from strong materials and is meant to withstand high pressure, temperature fluctuations, and corrosion environment. This strength adds up to more extended life or fewer replacements.
5. Standardization:
The JIC standards ensure compatibility between different manufacturers, so components can be sourced and replaced quickly if need be.
Best Practices for Using JIC Fittings:
Jic Fitting:
To get the best performance out of fittings, there are set best practices:
1. Proper Installation:
The flared surfaces should be clean and free of debris before connecting them. The fittings must be aligned carefully to avoid cross-threading or damaging them.
2. Torque Specifications:
Jic Fitting:
Thirdly, the fittings should be tightened with torque specifications specified by the manufacturers. Over-tightening may damage them, and leaks may occur due to under-tightening.
3. Periodic Inspection:
Periodic inspections for wear, corrosion, or damage on the JIC are critical to avoid leakages and system failure. Early detection of such problems leads to prevention.
4. Avoid Contamination:
Jic Fitting:
Hydraulic fluid should not come into contact with dirt due to contamination by fittings and lines connected to them. Contaminated hydraulic fluid may lead to rapid wearing down of the parts, which may ultimately lead to failure of the system.
5. Compatibility Check:
Jic Fitting:
Make sure the fittings you would buy are compatible with the hoses and the tubes that exist in your system. Incompatible parts usually leak and lead to performance problems.
Conclusion:
Jic Fitting:
JIC is essential in most hydraulic and fluid transfer systems, offering reliability and ease of operation across different industries. Their flare design at 37 degrees ensures leak resistance, while their versatility makes them capable of fitting almost all applications, from automotive to aerospace. Understand their features, applications, and best practices on how to use JIC on your projects, and you can make informed decisions on using them.
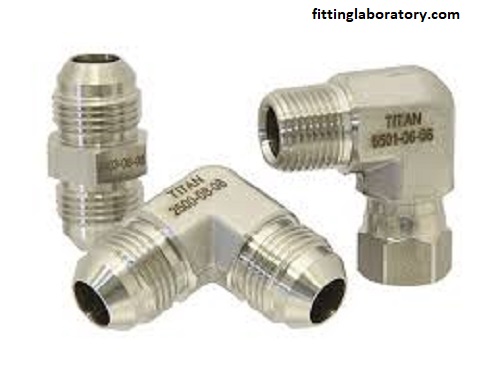
Proper installation and regular maintenance take time, but they improve the performance and therefore the life of hydraulic systems. However, the maturity of some industries has ensured that JIC continues to play a key role in reliable fluid transfer solutions. Whether you are experienced in using hydraulic systems or new to them, knowing the details involved in attachments will allow you to produce better to ensure reliability and performance on the job.